Why Choose One Cryogenic Transfer Hose Over Another?
By Igor Smola, Sales Engineer
Hoses are one of the unsung heroes of cryogenics. They aren’t directly responsible for the production or storage of cryogenic liquids, nor do they make headlines in the same way that innovations enabled by cryogenics do. However, hoses are found throughout cryogenic processes and in many products like MRI machines where movement and flexibility are required.
How else would we move the media?
Piping systems rely on flexible components to accommodate movement and absorb vibration while the nature of transfer systems often demands hoses which can be moved from place to place. Their use is so broad that hoses can appear interchangeable.
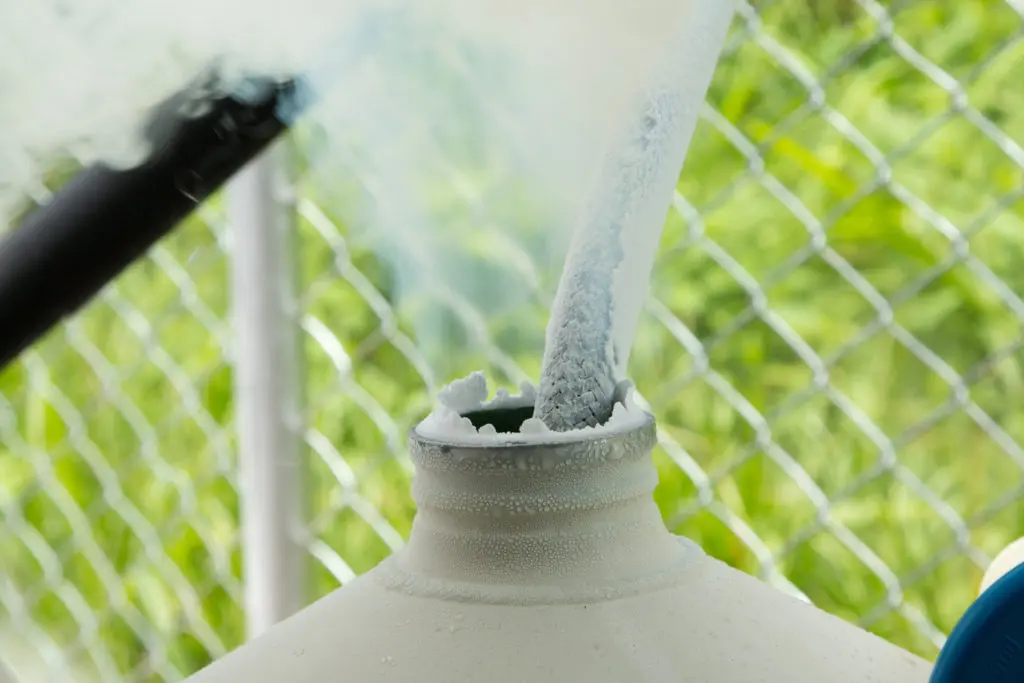
But will just any hose do?
While one stainless steel hose may look like any other, there are design choices and manufacturing processes, as well as cleaning and leak testing specifications, that would lead the informed observer—once again—to the conclusion that looks aren’t everything.
Knowing the application ultimately determines the variables. Here are some key design criteria:
- Annular hose design. Annular hoses, where corrugations are “stacked” parallel to one another, consistently achieve longer dynamic cycling than helical hoses, where corrugations have a screw-like appearance.
- Wall thickness. Using thinner strip metal makes a hose easier to bend. This may be desirable, first and foremost, for ease of installation, but also in tight spaces where a smaller minimum bend radius may be desired. (At Penflex we caution against looking to operate in line with minimums as this usually leads to less than maximum efficacy.) A heavier wall hose may be desired in certain cryogenic applications if corrosion is a concern: a thicker wall will last longer in a corrosive application than will a thinner wall.
- Compressed pitch. The greater the number of corrugations, or the higher the corrugation count, the more flexible a hose will be.
- Higher corrugation height. Increasing the height of the corrugations is another way to increase the flexibility. Many attributes play a role in the flexibility of a hose or braided hose assembly, and each one is taken into consideration individually as well as collectively when designing the right solution for a particular application.
- Armored ends. Sometimes hoses are designed with interlocked casing or armor near the end fittings to protect the hose from overbending, which can lead to premature failure. Overbending often occurs before a hose even goes into service, during installation.
- CGA Fittings. Penflex offers a full suite of cryogenic liquid transfer connections in line with Compressed Gas Association (CGA) V6.
- Vacuum jacketing. For some cryogenic applications, especially those involving LNG, adding a second hose enables users to maintain media temperatures within the inner hose by pulling a vacuum within the outer hose.
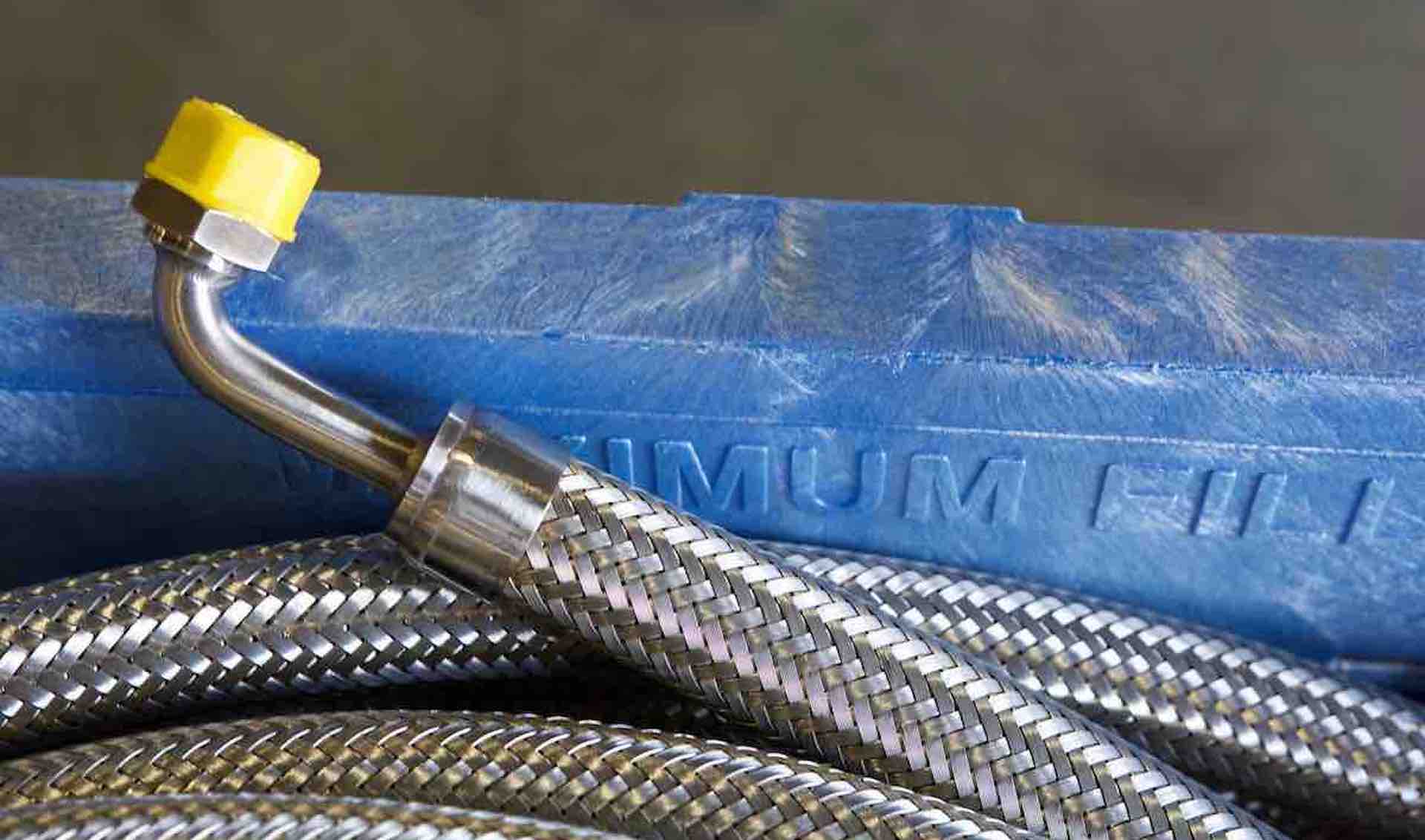
Procedures developed to deliver finished hoses cleaned, charged and ready for service include plugging the hose when cutting ends to prevent chips from getting inside and using tools reserved solely for stainless steel.
Welds are purged using argon gas, a proven process that enhances weld quality by decreasing—or even preventing— oxidation. This, in turn, maintains the corrosion resistance of parent materials, ultimately reducing leak rates in finished product.
Our welders are certified to American Society of Mechanical Engineers (ASME) Section IX, the industry’s highest standard. They have undergone rigorous training and years of experience to deliver the superior welds that help to ensure the cleanliness of cryogenic hoses. Once hoses pass visual inspection, a borescope is used to identify and remove any contaminants that may have entered the hose as a final step before leak testing.
Then, a mass spectrometer with helium tracer gas is used to test the cryogenic transfer hoses. First used to test for leaks in uranium plants as part of the Manhattan Project during WWII, helium mass spectrometer testing is among the most accurate methods of leak detection, capable of detecting leaks as small as 10E-9 cubic centimeters per second.
As metal hose is the sole means of transferring cryogenic media with minimal evaporation and without significant changes in temperature or pressure, Penflex has tailored its design and production processes to best serve this exciting market.
This article on cryogenic transfer hoses originally ran in the Cryogenics Society of America’s Cold Facts magazine, Vol. 27, No. 2.
To print, please click here.
About Penflex
Founded in 1902, Penflex is an ISO 9001-certified manufacturer of flexible metal piping solutions, offering a broad range of metal hose, braid, bellows and expansion joint products along with complementary services, including sales and welder training, engineering support, prototyping, testing and contract braiding. Known for quality and durability, our products are sold into multiple, unsynchronized vertical markets all over the world. Based in Gilbertsville, PA, Penflex maintains a warehouse in Houston, TX and operates a second manufacturing facility in Ho Chi Minh City, Vietnam.
More Articles
New Clean ID hose Streamlines the semiconductor supply chain
February 11, 2025
Penflex Receives CRN Approval for Metal Hose Assemblies Used in Turnaround Projects
October 29, 2024
Technology Advances Yield Clean ID Hose
May 29, 2024