Tạo hình và hàn ống
Tại Penflex, ống kim loại được sản xuất từ dải thép không gỉ. Các cuộn dây liên tục được tạo thành ống và đường nối dọc được hàn. Mối hàn là mối hàn đối đầu xuyên toàn bộ. Mối hàn được hàn TIG. “TIG” là viết tắt của “Tungsten Inert Gas”. Vonfram là điện cực có nghĩa là nó là vật dẫn được sử dụng để mang dòng điện (cung cấp nhiệt cho quá trình hàn). Vonfram không bị tiêu hao trong quá trình hàn, do đó không có vật liệu nào từ vonfram được chuyển vào ống. Tất cả các vật liệu nóng chảy vào mối hàn đến từ chính dải. Không có vật liệu phụ nào được thêm vào mối hàn dọc. Khí trơ được sử dụng trong quá trình hàn là argon. Trơ có nghĩa là "không phản ứng". Khi nhiệt độ cao từ dòng điện hàn làm nóng chảy hai mép của mối nối khi có oxy, oxy này sẽ phản ứng với các nguyên tố trong kim loại tạo thành oxit. Ảnh hưởng của quá trình oxy hóa này là một khu vực có thể dễ bị ăn mòn hơn so với kim loại cơ bản bên cạnh. Vì lý do này, argon được đưa vào khu vực ngay nơi đặt điện cực. Đây được gọi là "tẩy" mối hàn. Dòng argon đẩy tất cả oxy ra khỏi đường để nó không thể phản ứng với kim loại. Vì argon là “khí trơ” nên nó không có bất kỳ tác dụng nào. Tại Penflex, bên trong ống được “tẩy hoàn toàn” khi argon được đưa vào và tích tụ trong thể tích kèm theo của ống. Tương tự như vậy, argon chảy trong khu vực vonfram ở bên ngoài ống, nhưng vì khu vực này mở ra khí quyển nên dòng argon phải không đổi; nó không tích lũy.
Sự chuyển đổi từ ống sang ống: Phương pháp uốn cong cơ học
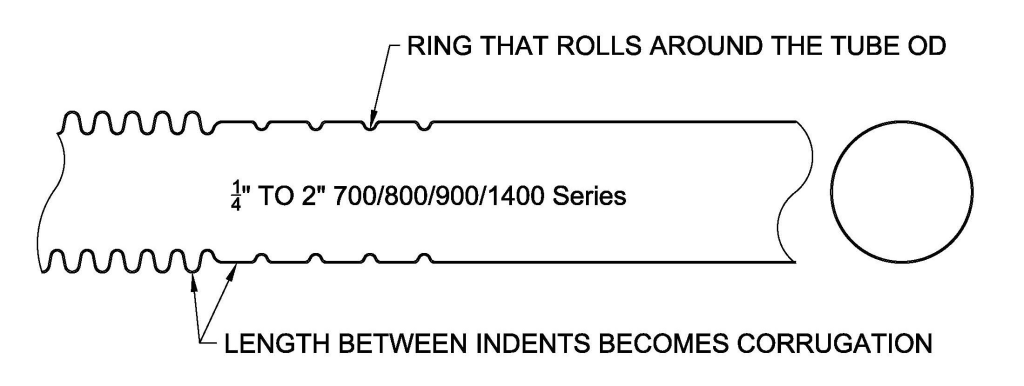
Độ dày kim loại cơ bản được sử dụng trong các kích thước ống sóng từ 1/4 "đến 2" thay đổi từ .008 "đến .024" tùy thuộc vào nhu cầu chống lại áp lực hoặc ăn mòn. Tỷ lệ giữa độ dày kim loại và đường kính của ống tương đối lớn, do đó ống hơi cứng về độ lệch và mạnh về khả năng chống lại sự nghiền nát. Vì lý do này, các kích thước ống từ 1/4 "đến 2" có thể được hình thành bằng cách "ghi điểm từ bên ngoài": Khi ống được đưa vào bộ xếp giấy, nó đi qua một "vòng cắt" cuộn xung quanh nó, đẩy vào ống. Kết quả là một "điểm số" hoặc một chút "cổ chai" của ống trong các khoảng thời gian đồng đều khi mỗi phần tiến lên. Những khu vực “dài cổ” này cuối cùng sẽ trở thành “thung lũng” của sự hư hỏng. Dụng cụ được thiết kế để có bán kính trơn nhẵn để giảm thiểu sự tập trung ứng suất. Tiếp theo, một cặp dụng cụ “hình chữ C” trên máy gấp nếp được gọi là “hàm” kẹp vào ống ngay trên phần “đã ghi”. Sau đó, bộ hàm thứ hai kẹp vào phần “cổ xuống” liền kề. Một trong những bộ hàm này đứng yên và bộ còn lại di chuyển về phía bộ hàm đứng yên. Điều này làm cho vật liệu ống giữa các hàm “thắt chặt” thành một hình dạng cong để tạo ra các nếp gấp. Khoảng cách giữa các “vết cắt” xác định chiều dài của vật liệu có sẵn để tạo thành nếp gấp: Khoảng cách giữa các “vết cắt” càng dài, nếp gấp càng “cao”. Chiều cao của nếp gấp liên quan đến ID của ống đôi khi được gọi là "hồ sơ" của ống. Đó là, chúng tôi nói rằng một ống có “cấu hình cao hơn” so với ống khác nếu sự khác biệt giữa OD và ID của nó lớn hơn sự khác biệt tương tự trên ống kia.
Quá trình chuyển đổi từ ống sang ống: Phương pháp hình thành bằng thủy lực
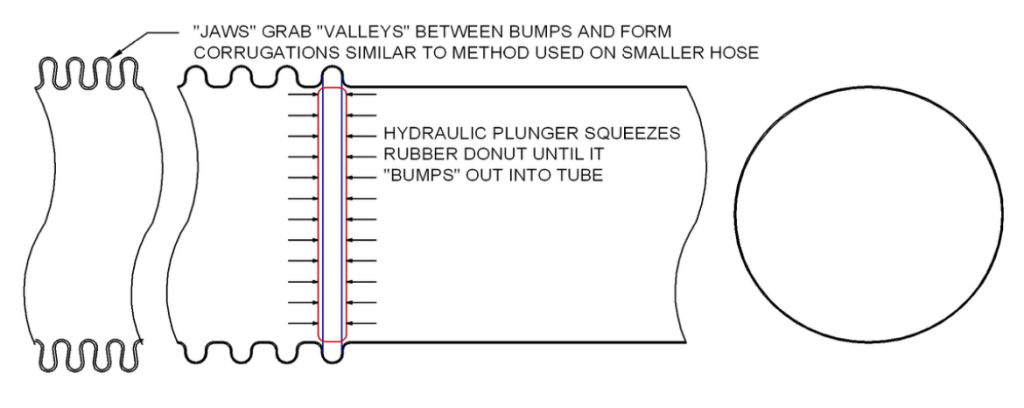
Khi kích thước ống ngày càng lớn, độ dày của “thành” ống sẽ rất mỏng tương ứng với đường kính. Ống không quá “cứng” so với các kích thước nhỏ hơn. Trên thực tế, ống có thể được bóp bằng tay với ít lực và tạo thành hình bầu dục. Nếu bạn cố gắng sử dụng quy trình “cắt vòng” trên ống này để tạo thành ống, các thành ống sẽ “thắt lại” hoặc sụp đổ ở giai đoạn cắt. Vì lý do này, các ống kích thước lớn hơn được hình thành thay vì đẩy kim loại “ra ngoài” khỏi ống chứ không phải vào trong. Điều này có thể được thực hiện theo một số cách. Tại Penflex, ống được trượt qua một "cao su va đập" có hình dạng giống như một chiếc bánh rán vừa vặn bên trong ống. Một pít tông thủy lực ép bánh rán. Khi nó phẳng ra, nó cũng mở rộng ra ngoài theo đường kính của nó và đẩy vào thành ống, kéo vật liệu từ ống lên thành một "chỗ phồng".
Khi áp lực lên pít tông được loại bỏ, bản chất đàn hồi của "cao su va đập" cho phép nó trở lại hình dạng ban đầu. Ống tiến một khoảng nhất định và sau đó quá trình này được lặp lại. Tại Penflex, từng nếp gấp riêng biệt được hình thành tại một thời điểm. Chúng tôi gọi phương pháp này là “Hình thành bằng thủy lực” bởi vì một pít tông thủy lực được sử dụng để tạo ra lực đẩy vật liệu ra ngoài để tạo thành các nếp gấp. Không nên nhầm lẫn “hình thành thủy lực” với một phương pháp tạo hình kim loại khác được gọi là “tạo hình thủy lực”. Trong quá trình tạo hình bằng thủy lực, lực được sử dụng để đẩy kim loại ra ngoài để tạo nếp gấp được tạo ra bởi nước thay vì một bánh cao su nén. Áp lực nước từ bên trong ống đẩy kim loại vào một “khuôn” ở bên ngoài ống, tạo ra hình dạng của “vết sưng”. Hydro-shape có thể được sử dụng để tạo thành các nếp gấp riêng lẻ, hoặc trong một nhóm gồm nhiều “bướu” cùng một lúc ở dạng “nhiều trạm”. Thông thường, phương pháp tạo thủy lực được sử dụng trên ống có thành mỏng hơn và ống có thành dày hơn được tạo bằng phương pháp thủy lực “cao su va đập”. Tại Penflex, tất cả các ống có kích thước 2-1 / 2 ″ trở lên đều được chế tạo bằng phương pháp thủy lực “cao su chống va đập”. Sau khi các va chạm được đưa vào trong ống, các hàm cố định và có thể di chuyển được sẽ kẹp lấy ống trong các “thung lũng” giữa các nếp gấp. Các hàm có thể di chuyển ép về phía các hàm đứng yên để tạo thành các nếp gấp. Bước này trong quy trình tương tự như được sử dụng trong phương pháp uốn nếp cơ học.
Ống thành mỏng kết hợp tạo hình và uốn ống: Quy trình #3 - Phương pháp liên tục (P3)
Phương pháp tạo hình ống thứ ba tương tự như quy trình P1 vì nó cũng tạo hình từ bên ngoài một cách cơ học. Không giống như các quy trình P1 và P2, bắt đầu với một chiều dài riêng biệt của ống được hình thành, được tải và di chuyển theo kiểu tương tự thông qua một giai đoạn tạo hình tại một thời điểm, phương pháp P3 bắt đầu với dải phẳng liên tục di chuyển qua ống tạo hình và hàn các trạm và sau đó trực tiếp vào các trạm tạo nếp gấp. Tại đây, các con lăn di chuyển xung quanh bên ngoài của ống trong khi ống chuyển động với tốc độ không đổi qua các trạm tạo hình. Độ dày của dải được sử dụng mỏng hơn nhiều so với quy trình P1, vì vậy “công việc” được thực hiện từ bên ngoài để tạo hình các nếp gấp phải được thực hiện theo nhiều bước nhỏ để tránh làm hỏng ống. Vì lý do tương tự, bên ngoài của ống cũng phải được bôi trơn nhiều hơn so với quá trình P1 (để tránh ứng suất trên ống có thành mỏng), do đó, có một trạm "xả" trong dòng. Thực tế là dải được đưa vào dây chuyền liên tục cho phép sản xuất chiều dài dài hơn. Trong quy trình P1, chiều dài của ống được giới hạn bởi chiều dài của ống thẳng có thể được sản xuất trong bước đầu tiên của quy trình. Trong quy trình P3, chỉ giới hạn ở kích thước của “nồi” thu nhiệt mà ống thành phẩm được cuộn vào và các vấn đề thực tế về xử lý, thử nghiệm và kiểm tra cuộn dây đó.