Process Improvements Yield Clean ID Hose
By Robert P. Barker, President, Penflex
The manufacturing of metal hoses commences with thin material strips that are brought together to form a straight tube. Corrugations are then introduced, enabling flexibility and adaptability across various applications. Different methods are employed to create these corrugations: Hydroforming utilizes high-pressure water to push the material from the inside into dies, determining the shape of the corrugations. Mechanical forming involves the use of dies split into two sections of a ring, which either squeeze the tube to form a bulge or employ a series of rotating dies around the tube to create corrugations progressively.
While both production methods yield quality hoses for most applications, they possess tradeoffs that render them unsuitable for certain uses. In helium-based cryogenic applications, a critical concern arises: “Can a hydroformed hose ever be entirely free of moisture?” Hoses carrying helium demand thorough cleaning to eradicate detrimental contaminants when produced via hydroforming. Contaminants encompass moisture, oils, greases and solvents, as well as any residues from welding or cutting. However the cleaning process itself can lead to recontamination. For instance, while a cleaning agent may remove oil, it might leave solvent, acid, or alkali residues.
Frequently, specifications for metal hose assemblies necessitate post-production cleaning. These specifications detail methods such as cleaning with a spar nozzle or interior mandrel using aqueous solutions, which involve extensive labor followed by draining and oven drying. Additional testing for hydrocarbons or particulate matter is also conducted to ensure cleanliness. However, such post-production processes and tests can be eliminated. Mechanical forming, as employed in Penflex’s CL3 process, generates hoses devoid of internal water, oils, solvents and tooling marks. These hoses are clean and devoid of stress risers.
The CL3 mechanical forming process pioneered by Penflex represents a seismic shift in the realm of cryogenics. Its profound impact reverberates across diverse applications within this critical industry. Consider, for instance, the transportation of liquefied gases like helium or hydrogen ҄ where cleanliness and purity are non-negotiable. Some traditional manufacturing methods pose substantial risks to these sensitive substances. However, the CL3‘s precision-engineered approach ushers in an era of unparalleled purity within hoses. This innovation isn’t merely about eliminating postproduction cleaning: it’s a fundamental paradigm shift. The absence of moisture exposure during mass spectrometer leak testing ensures the reliability of critical equipment ҄ a game-changer for research, medical, and aerospace applications reliant on accurate cryogenic systems.
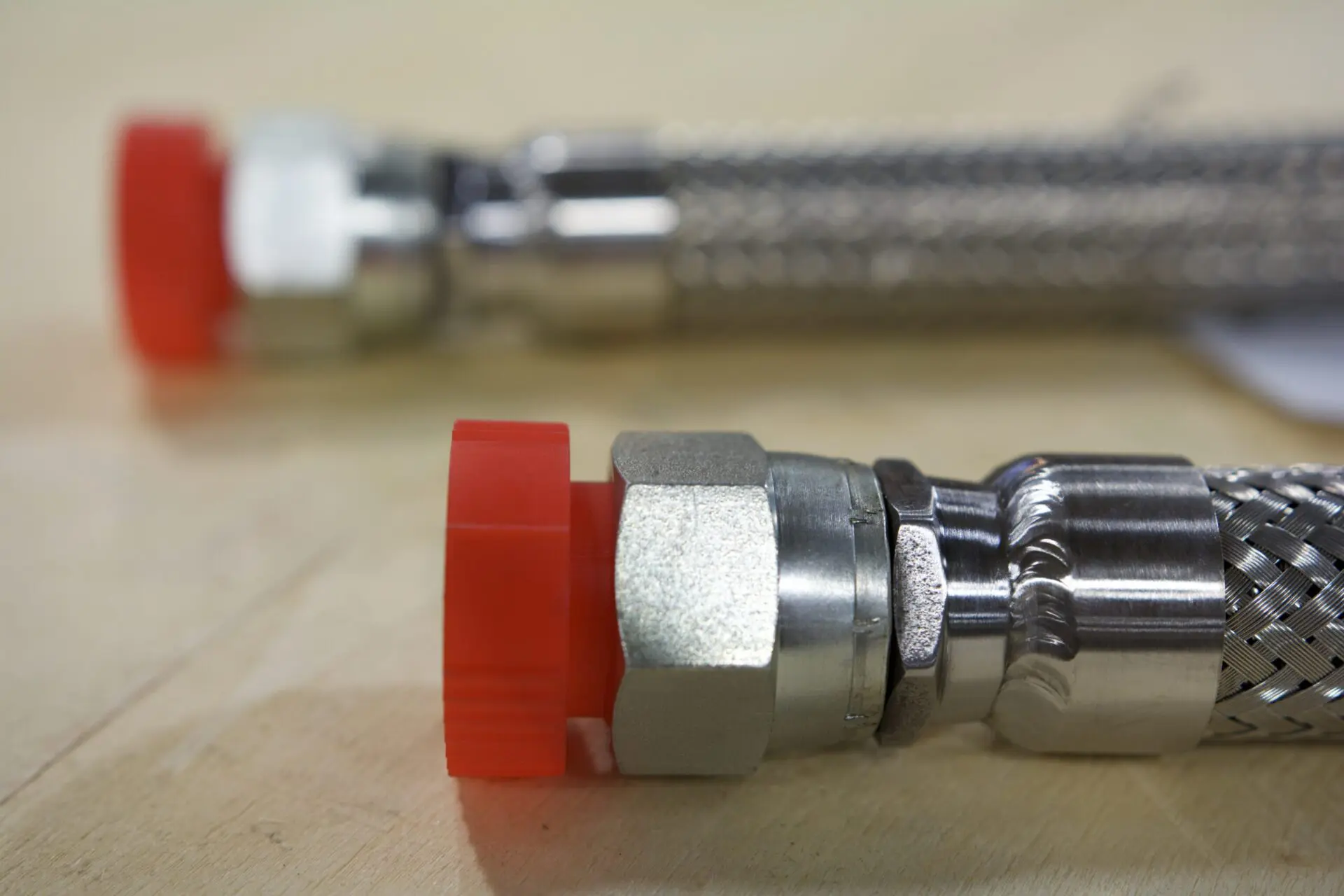
Moreover, the CL3 process’s streamlined production and reduced need for additional cleaning makes it a catalyst for operational efficiencies across the cryogenic supply chain. As industries push the boundaries of low temperature apphttps://www.cryogenicsociety.org/cold-factslications, the CL3 process emerges as a cornerstone of reliability, setting new benchmarks for cleanliness, efficiency and safety incryogenics.
This article originally ran in Cold Facts, The Magazine of the Cryogenic Society of America, Buyer’s Guide 2024.
About Penflex
Founded in 1902, Penflex is an ISO 9001-certified manufacturer of flexible metal piping solutions, offering a broad range of metal hose, braid, bellows and expansion joint products along with complementary services, including sales and welder training, engineering support, prototyping, testing and contract braiding. Known for quality and durability, our products are sold into multiple, unsynchronized vertical markets all over the world. Based in Gilbertsville, PA, Penflex maintains a warehouse in Houston, TX and operates a second manufacturing facility in Ho Chi Minh City, Vietnam.
More Articles
New Clean ID hose Streamlines the semiconductor supply chain
February 11, 2025
Penflex Receives CRN Approval for Metal Hose Assemblies Used in Turnaround Projects
October 29, 2024
Technology Advances Yield Clean ID Hose
May 29, 2024