Leak Detection Methods
There was a time when Penflex used helium tracer gas for leak detection. Helium was used because its molecules are small, smaller than air molecules. We used to test each piece of metal hose under water and watched for bubbles escaping to the surface.
Although, at the time, we had determined this was the best way to identify and locate a possible leak (evidenced by bubbles), there was also a disadvantage. In this leak detection method, small leaks form bubbles at a slow rate. It takes a good eye and significant time to ensure there are no leaks. In addition the process sometimes inadvertently introduced water into the hose. We were eager to incorporate a leak detection method that was more efficient.
Once we learned of a new method in leak detection, we were eager to incorporate it into our testing process. This detection method uses hydrogen as the tracer gas and is based on a microelectronic sensor technology known as MIS-FET. The sensor is a field effect transistor in an integrated circuit. The gate electrode of the transistor is made of a hydrogen absorbing metal alloy (metal hydride). When this device is exposed to hydrogen, the gas molecules absorb on its surface, dissociate into hydrogen ions (protons) and diffuse rapidly into the gate metal. The absorption of hydrogen ions affects the work function (surface potential) of the metal, which gives the same effect as if the gate voltage of the transistor was changed. The electrical output signal from such sensors must undergo signal interpretation in order to give reliable measurements. This is done by a microprocessor in the instrument.
Hose sizes with nominal inside diameters from 12” down to 2-1/2” are manufactured in mill lengths approximately 25 feet long. These hose sections are filled with the 5%-95% hydrogen-nitrogen mix, the ends are capped and a probe is manually moved directly along the weld seam at a rate of 5 seconds per foot.
If there should be a leak anywhere along the weld seam, the hydrogen gas from inside the hose finds its way through the hole by “diffusion.” The hydrogen detector unit is calibrated to a leak alarm level of .0088 cc/sec.
Hose sizes with nominal inside diameters ranging from ¼” to 2” are manufactured in mill lengths approximately 50 feet long. In order to test these longer hose sections more efficiently, an automated system is used. A “tram” moves a short section of PVC pipe along the entire length of the hose. A special probe “sniffs” the volume of gas which accumulates inside the PVC tube which is sliding along the hose.
If gas leaks out from the weld seam, the concentration of hydrogen in the void around the hose will increase. The hydrogen detector unit is calibrated to a leak alarm concentration of 10 ppm hydrogen. An audible alarm sounds when a leak is encountered and the moving “tram” stops. At this point, the tester uses the manual probe to locate the leak and mark it so that it can be cut out after the test.
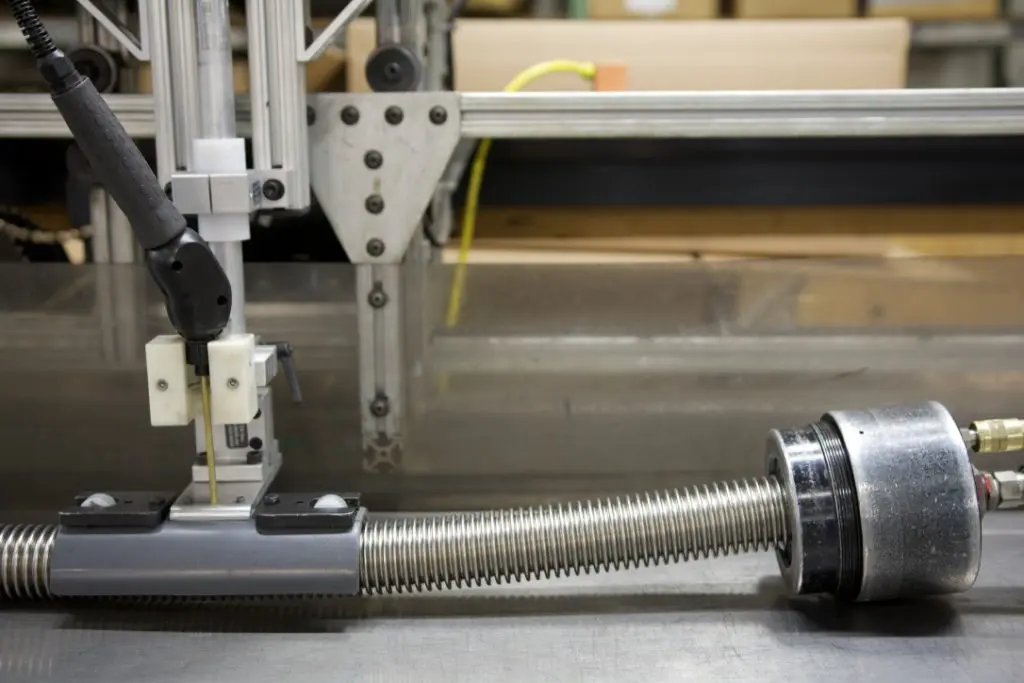
Hydrogen leak test being administered in Penflex’s Gilbertsville, PA headquarters.