Alloy Selection in Ammonia Service
Feeding the World’s Population
Between 1900 and 2000, the world’s population grew from 1.6 billion to 6 billion. Today, it registers at 7.9 billion.[1] Something happened in the 20th century that allowed this great explosion of population to take place.
While a mix of inputs are required for plant growth, nitrogen is considered the most important given how much is required. As such, crop yields are limited by the amount of nitrogen available and farmers in centuries past relied upon manure to augment the work of nitrogen-fixing bacteria in the soil to deliver this critical element.
In the early 1900s, a pair of German chemists discovered how to synthesize ammonia (NH3)–a nitrogen-hydrogen compound–and thereby boost the amount of nitrogen available to plants. Inorganic nitrogen fertilizers, often injected into the soil as liquid ammonia, allowed for great increases in crop yield, the kind of increases that could spur a population explosion.
Given the role it plays in feeding the world’s population, ammonia is one of the most widely produced chemicals. One hundred and eighty million metric tons are produced annually.[2] With the world’s largest population, it may come as no surprise that China is the top producer. India, Russia and the United States follow.[3]
Ammonia is also used in commercial refrigeration systems and in household cleaners, and its use as a potential hydrogen fuel source is a popular topic of conversation as well
Ammonia as a Health Hazard
Direct exposure to ammonia in high concentrations is hazardous to human health and numerous government agencies and industry associations have developed various specifications, procedures and training sessions to limit leaks. These efforts, along with correct handling and preventive maintenance, have kept incidences of leaks and human injury to relatively low levels.
Interestingly, Fertilizer Grade Ammonium Nitrate is listed as a chemical of interest in the U.S. Department of Homeland Security’s Chemical Facility Anti-Terrorism Standards.[4] While this signals the potential for its use as a chemical weapon, for the purposes of this bulletin, it underscores the importance of safety in the design and operation of ammonia piping and transfer systems.
Metal Hose in Ammonia Service
Common applications for hoses in these systems include connections between fixed loading and unloading systems, and in nurse tank trailer, rail and truck transport. Metal is often the preferred material of construction given its chemical compatibility. Metal hoses also offer a more robust design given braid layers protect the inner core from abrasion and welding is the end fitting attachment method.
The 300 Series stainless steels are suitable options for most ammonia service applications, including those involving anhydrous ammonia, a liquid solution that is used both as fertilizer and commercial refrigerant. Anhydrous ammonia corrodes copper and zinc alloys and can also attack rubber and certain plastics.
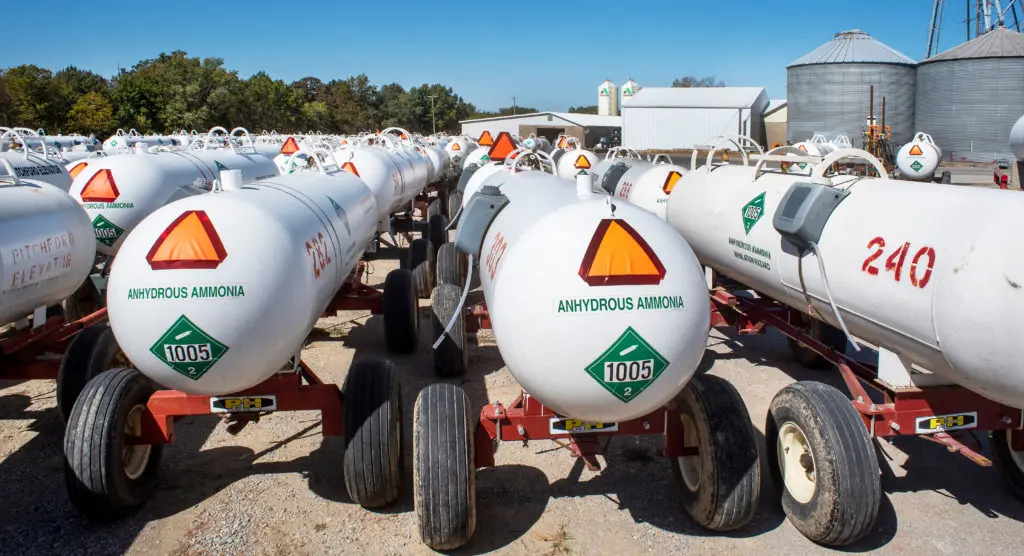
A gas at room temperature, anhydrous ammonia is cooled to its liquid state before being transported under pressure to its destination. When working with anhydrous ammonia gas at elevated temperatures, the 300 Series stainless steels are not recommended. Contact the factory for details about other options.
When working with ammonium bromide, ammonium sulfate or ammonium chloride in concentrations above 10%, 316L is recommended above 304 and 321 which are only partially resistant to these media.
For a more complete listing of alloy compatibility with ammonia have a look at our corrosion resistance chart.
Concerns Around Explosiveness
While ammonia is non-flammable, it can ignite in the presence of certain compounds, namely halogens, with explosive force. Chlorine and various chlorides are halogens, so great care must be taken to remove contaminants during production and to avoid their entry into the system during shipment, storage and installation.
Key precautions must be taken during manufacturing, and include removing any chips or debris from the inside of the hose after cutting and purging welds with argon gas. Welds and welders should be certified under ASME Section IX, the industry standard for quality welding.
Considerations on Stress Corrosion Cracking
In addition to being a potential ignition source, contaminants also exacerbate corrosion in a hose. With its strong affinity for water, it is important to prevent an influx of moisture into an ammonia piping system.
Chloride contamination from the ingress of water can reduce the service life given material sensitivity to these compounds. Stainless steel and chlorides are a pairing highly susceptible to stress corrosion cracking (SCC). This form of corrosion occurs at the intersection of a susceptible material, working or residual stress experienced above the SCC threshold, and a corrosive environment. Cracks may lead to leaks if not identified soon enough.
Regular inspection of hoses in ammonia service is important for identifying cracks, as well as damaged braid, deformation of the hose, cracked fittings, or traces of media on or around piping components that could indicate imminent failure.
Footnotes
[1] United States Census Bureau. U.S. and World Population Clock. Retrieved August 11, 2022 from https://www.census.gov/popclock/
[2] Alexander Tullo. 8 March 2021. Chemical & Engineering News. Is ammonia the fuel of the future?. Retrieved August 11, 2022 from https://cen.acs.org/business/petrochemicals/ammonia-fuel-future/99/i8
[3] Johnny Wood. 29 October 2021. Forbes. Scaling Ammonia Production For The World’s Food Supply. Retrieved August 11, 2022 from https://www.forbes.com/sites/mitsubishiheavyindustries/2021/10/29/scaling-ammonia-production-for-the-worlds-food-supply/
[4] Cybersecurity & Infrastructure Security Agency. Chemical Facility Anti-Terrorism Standards (CFATS). Retrieved August 11, 2022 from https://www.cisa.gov/chemical-facility-anti-terrorism-standards.